Comprehensive Tank Welding Evaluation for Industrial Safety and Regulatory Compliance
Making sure commercial safety and governing conformity within the world of container welding inspections is an essential facet of preserving functional stability and mitigating potential risks. The precise exam of weld high quality, material density, and general tank problem is critical in protecting against architectural failures and environmental threats. By delving into the ins and outs of comprehensive storage tank welding assessments, a deeper understanding arises of the multifaceted methods used to support market standards and promote security procedures.
Relevance of Container Welding Evaluations
Carrying out regular and extensive tank welding examinations is vital in ensuring the structural stability, safety requirements, and governing conformity of industrial tanks. These assessments play a critical function in determining any type of prospective problems or weak points in the bonded joints that can compromise the general stability of the tank. By spotting these problems beforehand, business can take proactive measures to address them promptly, therefore protecting against expensive repair work, environmental contamination, or, in the worst-case scenario, disastrous failures.
Regular tank welding evaluations likewise help companies abide by sector laws and criteria stated by authorities such as the American Oil Institute (API) or Occupational Security and Health Administration (OSHA) Failure to fulfill these demands can lead to penalties, legal effects, or even the suspension of operations. Tank Welding Inspection Service. For that reason, buying thorough storage tank welding evaluations not just safeguards the well-being of workers and the surrounding atmosphere but additionally safeguards the firm's reputation and profits over time
Secret Elements of Weld Top Quality Assessment
Making certain the top quality of welds involves a meticulous analysis of key elements that contribute to the architectural honesty and dependability of industrial storage tanks. One essential aspect of weld top quality analysis is the evaluation of weld infiltration. Appropriate penetration is essential as insufficient penetration can cause weld flaws and jeopardize the strength of the joint. Additionally, the weld's account must be analyzed to guarantee that it meets the specified requirements in terms of shapes and size. The visibility of any interruptions, such as splits, porosity, or incomplete fusion, have to be completely inspected as these can weaken the weld and increase the possibility of failure. Additionally, the total weld look is also an essential element of top quality analysis, as it can suggest the visibility of defects or inconsistencies in the welding process. By comprehensively evaluating these vital components, inspectors can help assure that bonded joints fulfill the needed requirements for security and regulatory conformity in commercial storage tank building.
Product Thickness Evaluation Methods
In the context of weld quality analysis, an essential facet to think about is the utilization of material density assessment strategies. Accurate dimension of product thickness is vital in making sure the structural integrity and safety of bonded containers. Numerous non-destructive testing (NDT) approaches are employed for analyzing material thickness, consisting of ultrasonic screening, radiographic testing, and magnetic bit inspection. Ultrasonic testing includes making use of high-frequency acoustic waves to establish material thickness by gauging the moment taken for the sound waves to take a trip via the material and reflect back. Radiographic testing makes use of X-rays or gamma rays to generate images showing material density. Magnetic fragment inspection is efficient for finding surface area and near-surface defects that may impact product density. These strategies not just help in evaluating the thickness of materials however likewise help in recognizing any kind of possible defects or gaps that might jeopardize the weld high quality and total honesty of the container framework. By Continue using these product density analysis strategies, sectors can make certain conformity with safety and security criteria and laws, therefore boosting total functional security and dependability.
Storage Tank Condition Exam Techniques
An important facet in preserving the integrity and safety and security of welded containers is the complete evaluation of container conditions with reputable inspection techniques. Tank problem examination techniques play an essential duty in guaranteeing the architectural stability and functional efficiency of industrial containers. Visual assessment is a primary technique made use of to evaluate the exterior condition of storage tanks, seeking signs of rust, leakages, or physical damage. Furthermore, non-destructive screening techniques such as ultrasonic testing and radiographic screening Read More Here are used to spot inner flaws, weld problems, and product destruction that may compromise the storage tank's efficiency. Tank Welding Inspection Service. Moreover, magnetic particle assessment can recognize surface area cracks and defects that are not noticeable to the naked eye. These evaluation approaches give valuable insights into the general wellness of the container, enabling early detection of potential problems and assisting in prompt maintenance or repairs to guarantee compliance with security guidelines and market criteria. Normal examinations making use of these approaches are essential for preventing catastrophic failures and ensuring the long-term reliability of welded containers.
Benefits of Normal Evaluation Practices
Normal evaluation techniques not only secure against prospective concerns discovered throughout tank problem examination techniques yet also act as aggressive steps in promoting the Find Out More structural stability and functional efficiency of welded storage tanks. By performing regular assessments, commercial centers can identify any type of indicators of corrosion, splits, leaks, or other flaws in the container welds promptly. This early detection makes it possible for prompt repairs or maintenance interventions, stopping tiny concerns from escalating into larger, much more expensive troubles that can endanger safety or lead to regulatory non-compliance.
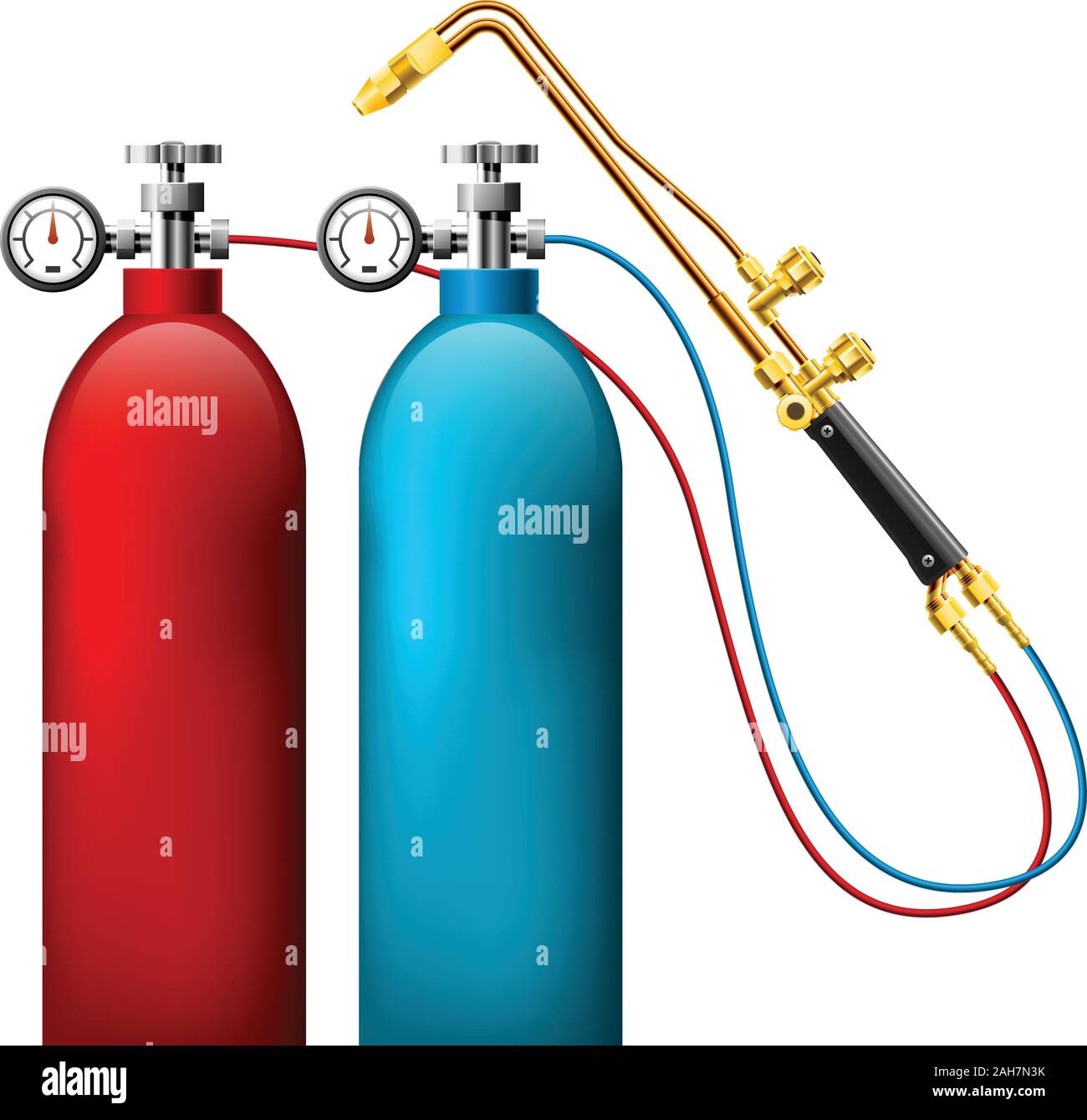
Conclusion

Finally, detailed tank welding evaluations are essential for guaranteeing commercial safety and regulative conformity. By performing regular assessments and analyses of weld quality, material density, and container condition, organizations can determine possible risks and avoid expensive crashes. Implementing a proactive method to assessment techniques can help maintain the structural stability of storage tanks, shield the setting, and ensure the safety of workers and the surrounding neighborhood.
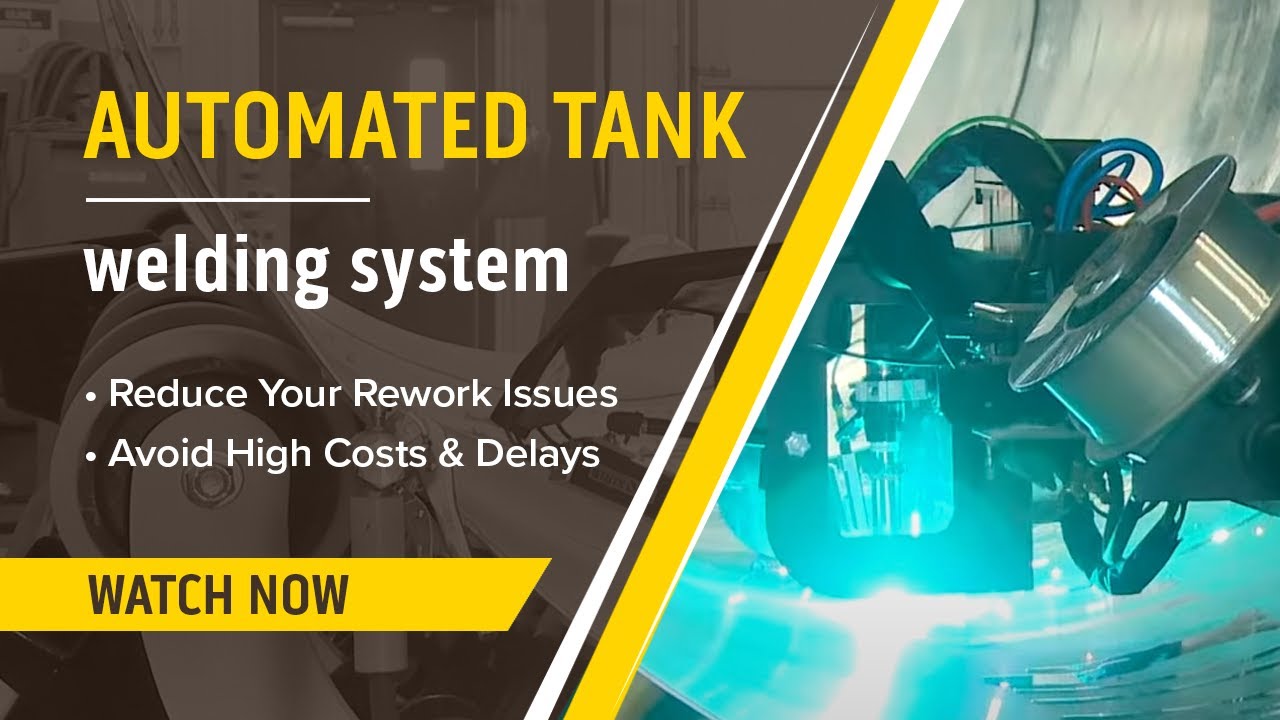